Pongsiri Kuresangsai, Ph.D. student
Advisor: Prof. Dr. Matthew O.T. Cole
Description of Project:
Conventional mechanisms, used to transfer energy, forces or generate desired motion, are constructed by connecting links using joints with rolling or sliding parts. This introduces effects such as backlash and friction, which can compromise the accuracy at micrometer scales. To overcome these effects, monolithic mechanisms may be constructed having compliant flexure-based joints that can achieve motion with higher repeatability and fidelity, even to sub-micron levels. Such compliant mechanisms have a number of other advantages. They require a reduced number of parts and can be made by single-process manufacturing such as 3-D printing or electric discharge machining. Constructing a mechanism as a single piece can also reduce time and costs. Flexure-based joints suffer less from wear or contamination and do not require lubrication. Even though flexure-jointed mechanisms can give high accuracy motion, the range of motion is limited by the elastic limit of the joints under deflection. Also the dynamic and kinematic behavior is more complex. For such mechanism, the analysis and optimization of designs is challenging.
Objective:
- To develop and verify non-linear dynamic models of the proposed mechanism
- To consider the design and application of controllers based on linearized models of the mechanism
- To investigate enhancing dynamic performance by utilizing non-linear dynamic models of the mechanism within the controller design procedure
- To implement and test controllers on the experimental system to verify and compare performance
Research overview
Many researchers have considered the design of flexure-based mechanism having workspace in micrometer scale. For widening the range of applications of flexure mechanism, we focus on designing flexure mechanism having large workspace in cm-scale but with compact mechanism that can operate at high accuracy for a large number of motion cycles.
A case study was undertaken involving the optimized design of a mechanism inspired by a having conventional five-bar linkage 2 DOF in XY plane and with 2 actuators. We use uniform beam joint to replace revolute joint because it is relatively simple to model and design and has good characteristics to achieve increased working area with low stress concentration.
In any equilibrium position for the flexure mechanism, the platform will rotate due to acting forces and bending moment applied through the connecting flexures. It is therefore desirable to design a mechanism for which rotation of the platform is as small as possible.
To undertake design optimization for flexure jointed mechanisms the use of nonlinear FEA models is possible. This can give high accuracy prediction of motion but is very computationally intensive. Therefore, a novel modelling approach having high accuracy even at large deformation configurations was developed. This approach was extended and applied for design optimization of a complete mechanism. The aim was to prevent rotation of the platform as much as possible. To validate the suitability of the proposed flexure modelling approach, result have been compared with nonlinear finite element method. The FEM results
then agreed closely with modelling approach, although a high accuracy FEM computation took approximately two hours compared with less than 10 seconds. Experimental results for the X-Y stage confirmed the effectiveness of the optimized design.
In the proposed work, this flexure modelling approach will be extended for use in dynamic models of the whole mechanism. Verification of the model can be made by frequency response testing approach. As the dynamic model will be complex and have some uncertainty a robust control approach will be required.
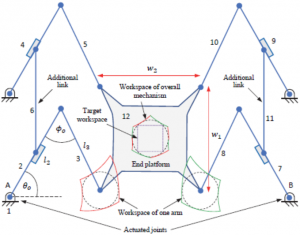
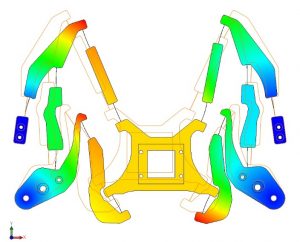
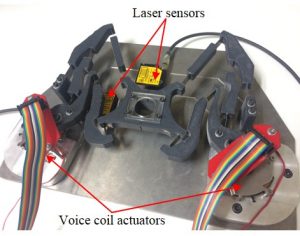
Acknowledgment:
This work was partially funded by the Chiang Mai University Mid-Career Research Fellowship program and Center of Mechatronic System and Innovation. Pongsiri Kuresangsai was supported by the RGJ-PhD scholarship program under the Thailand Research Fund and by a Ph.D. Studentship and TA/RA Scholarship from the Graduate School, Chiang Mai University.