Chawalit Khanakornsuksan, Ph.D. student
Assoc. Prof. Theeraphong Wongratanaphisan
Description of Project:
Parallel Kinematic Manipulators (PKM) have gained wide attention over past decades. Many researchers have developed PKMs to overcome some limitation of traditional serial robots. However, there are major drawbacks of PKMs such as small workspace, low dexterity and singularities. These are challenging problems that need to be addressed during the design. Cable Driven Parallel Robots (CDPRs) are a special class of PKMs whose actuated limbs are cables instead of rigid-linked actuators. All cable are attached to a mobile platform which hosts robot’s end-effector and the other ends are wound in fixed reels installed on a fixed base. Positions and orientations of the mobile platform can be attained by controlling the length of those actuating cables. The benefits of the cable actuation are its simple form of producing force, light weight, and relatively large actuating range resulting in large workspace. One of the promising applications of CDPRs is for the design of locomotion device as it can provide wide motion range with very light weight.
Objective:
As the cable-driven parallel robot has great potential for use in many applications, this study aim explorer that possibility. The purpose of the study is two fields:
- To introduce the new gait mechanism concept which is driven by cables in an end-effector type configuration. Conceptually, the user places their feet on a moving platform which is driven by a number cables during the gait motion. This machine can generate 3 DOF motion of the moving platform: ( x- and y- position and orientation in a vertical plane). The robot would be designed to suit rehabilitation task which is to produce a smooth gait motion for user with different physical parameter such as height and weight.
- Derive a method to optimally design the cable-driven gait generating mechanism. The outcome of study should allow us to indicate, in an optimal sense, what the locations of the cable attachment point on the moving platform and ground should be. The design targets are defined in terms of reducing cable tensions under applied external forces from user weight during the motion. Uncertainties due to external forces applied on the platform will be taken into account.
Scope of the study
- Analyze the gait motion and propose a suitable configuration of cable-driven gait generating mechanism which will be a platform for study. The study focuses on a non-redundant type cable-driven robot.
- Optimally determine the location of cable attachment points using PSO optimization technique.
- The motion of the mechanism is confined to a vertical plane.
Assumptions
- The weight of the cable will be neglected. Hence it will be assuming in the kinematic and force analyses that the cables are adjustable length linear elements.
- The moving platform is considered as a rigid body.
Optimal Design of a Hybrid and Fully Cable Driven Parallel Robot
In this thesis, two new automated gait mechanisms based on a cable-driven parallel kinematic mechanism are introduced: 1) a hybrid cable driven robot with 2 cables and one rigid moving link and 2) a 4-cable planar parallel robot (4CDPPR). Both mechanisms can generate three degrees of freedom (DOF) gait pattern motion of a moving platform (two translational and one rotational motion in a vertical plane) for normal walking gait.
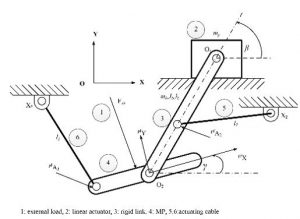
The first proposed mechanism, called the “hybrid cable driven planar parallel robot (HCDPPR)” , Fig. 1, was designed with two cable and one rigid link in order to maintain the number of degrees of actuation equal the number of degrees of freedom. The cables were designed to take only the tension force and the rigid link can take both tension and compression loads. A method was proposed to optimally locate the cable attachment points on ground and moving platform while keeping the cable tensions minimized in optimal sense. With the current design configuration, the results suggest that the cable attachment points on the ground should be at the waist level and the cable attachment points to the foot support should be below the joint of the connecting rod. In this configuration, constraints on optimized parameters were also be imposed in order to avoid cable and user interference.
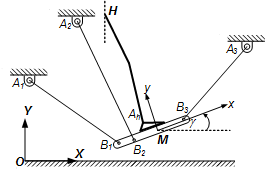
The second proposed mechanism employed only cables as actuating members. A method for the gait generating dimensional synthesis of cable driven planar parallel robots mechanism was proposed, Fig. 2. Two configurations have been considered. Firstly, a suspended 3-cable mechanism which makes use additional force from gravity as a virtual cable downward force. To optimally locate the attachment point, Particle Swarm Optimization (PSO) algorithm has been used to minimize cable tensions. The results showed that the optimal cable attachment locations are usually very high above ground which made structure of the mechanism very large and unrealistic. Due to the limit of space for installation, the range of cable attachment parameters are reduced to realistic values. In addition, to avoid body interference, the safety boundary constraints are included in the optimization algorithm.
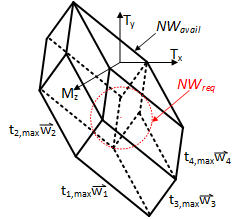
Realistically, the mechanism must be designed to take into account the range of unpredictable external forces that can act on the platform. The concept of graphical representation by polygon is applied to optimization algorithm to find the minimal polygon’s shape which can cover the desired wrench. The 4CDPPR system was used to show the behavior of the algorithm concept. For the whole range of motion, two wrench boxes were used to represent two different level of external force range (high and low) separated by two regions. The high-force region corresponds to the stance phase and the low force region represents the swing phase. In the optimization process we first randomly select the optimized parameters that a wrench closure workspace (WCW) exists. This will ensure that solutions for the polyhedra to enclose the wrench boxes can be found, Fig. 3. Then the PSO algorithm, Fig. 4, was set to begin finding the optimal parameters. It was shown that the proposed method that solutions in wrench feasible workspace (WFW) may be found by relaxing the size of the polyhedra. The size of polyhedra is related to the magnitude of maximum cable tension used in the objective function. By reducing the size of the feasible polyhedra, the optimal tension force can be obtained. Finally, our intuition is that the same approach can be applied to the dimensional synthesis of other prescribed trajectories as well as fully constrained systems with arbitrary number of cables.
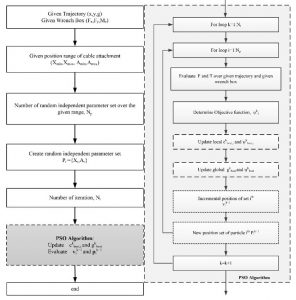
Acknowledgment:
This research was financially supported by The Royal Golden Jubilee Ph.D. Program (RGJPHD) Scholarship no. PHD/0101/2552 1.M.CM/52/G.1. The work was performed at the Motion and Control Laboratory, Chiang Mai University, Thailand.
Publication
Chawalit Khanakornsuksan and Theeraphong Wongratanaphisan ”Optimal Design of a Hybrid Cable Driven Parallel Robot for Desired Trajectory and Force”, on 2018 International Conference on Mechatronic, Automobile, and Environment Engineering (ICMAEE 2018), Chiang Mai, Thailand, 7-9 July 2018
Chawalit Khanakornsuksan and Theeraphong Wongratanaphisan ”Design Optimization of a Suspended Cable-Driven Gait Generator using Three Cables”, on Joint Symposium on Mechanical-Industrial Engineering and Robotics (MIER 2017), Chiang Mai, Thailand, 16-17 November 2017
Chawalit Khanakornsuksan , Pinyo Puangmali and Theeraphong Wongratanaphisan,”Design of a Hybrid Cable- driven Foot Platform Device”, proceeding on The 5th TSME International Conference on Mechanical Engineering, Chiang Mai, Thailand, 17-19 December 2014