by Prapon Ruttanatri, Ph.D. student
Advisor: Assoc. Prof. Dr. Matthew O.T. Cole
Description of project
Active control of structural vibration in machining processes to prevent dynamic instabilities and chatter is the main issue for this project. A controller design is proposed based on a multi-mode description of flexible structure dynamics combined with cutting process equations that capture time-delayed feedback effects. A method for robust delayed-state feedback control synthesis is presented based on Lyapunov-Krasovskii functionals (LKFs).
Objective
To develop and compare controller design methodologies for active control of regenerative vibration in machining processes in order to improve/increase operating regions for stable cutting. The main focus is on the use of modern robust controller design methodologies and new techniques for controller design based on combined models of machine structure flexibility and cutting force generation mechanisms.
Hardware-in-the-loop evaluations overview:
The experimental system used for this study (Fig. 1) has been designed to exhibit two main structural resonances and is dynamically similar to an AMB-equipped milling spindle that exhibits significant cutting tool flexibility. The main structure is a flexure-pivoted beam connected to an end-mass through another flexure pivot. Two non- contact electromagnetic actuators are used to apply forces to the structure. Hardware-in-the loop simulation and controller testing for machining vibration can be undertaken based on the configuration shown in the block diagram Fig. 2. In this scheme, actuator 2 is an auxiliary actuator used to apply a simulated cutting force that is computed in real-time using a cutting force model implemented within the control hardware. This also requires real-time measurement of the “tool” displacement. Actuator 1 is the control actuator and is used to apply the stabilizing control forces. Note that, as the cutting force model is implemented digitally on the control hardware, the cutting model can be selected freely, subject to limits of actuator force capacity and bandwidth. Displacement of the structure can be measured by two non-contact sensors positioned close to the actuators. Additional vibration measurements are obtained by strain gauges at the flexure locations. Integration of strain sensing in spindle bearing guides has been considered for the purpose of tool deflection compensation. However, in the present case the signals provide dynamic state information related to tool deflection that can be used for feedback control of vibration. Displacement measured at the cutting location is used for calculation of the simulated cutting force but is not used for feedback. Full state information is obtained by combined use of the displacement and strain sensors located away from the “tool” end.
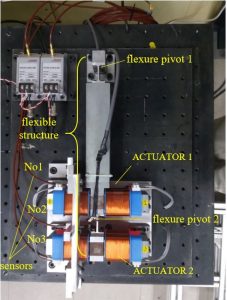
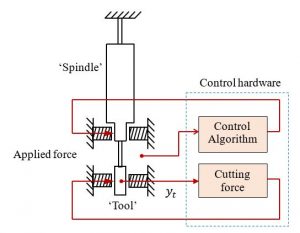
Publication:
- Prapon Ruttanatri, Matthew O.T. Cole and Radom Pongvuthithum, “Stabilizing Active Vibration Control of Machining Processes Based on Lyapunov-Krasovskii Functionals for Time-Delay Systems”, The 7th TSME International Conference on Mechanical Engineering, Chiang Mai, Thailand, page no. 152, December 13-16, 2016
- Prapon Ruttanatri, Matthew O.T. Cole and Radom Pongvuthithum, “Structural vibration control using delayed state feedback via LMI approach – with application to chatter stability problems” SAGE
Acknowledgement:
This work was partly supported by the RGJ-PhD scholarship program under the Thailand Research Fund (grant number PHD/0089/2553).